When to use Norklad 100-UV: 100% solidsis recommended for warehouses, kitchens, restrooms, and other areas where either a high build clear product is needed or where a decorative filled floor is desired. Standard packages are packaged in 1.5-gal kits. It must be applied quickly and skillfully with a notched squeegee by a professional or there is a high likelihod that it will cure faster than it can be applied. Standard packages are in pre-measured kits and should be mixed as supplied in the kit. ULTIMATE ELONGATION: 4.1% There are no harmful organic vapors (VOCs) like you experience with urethane application. FLEXURAL STRENGTH: 5,400 psi @ ASTM D790 Before recoating or topcoating, check the coating to insure no epoxy blushes were developed (a whitish, greasy film or deglossing). The material in the transfer pail is now ready to be applied onto your basecoat. It is 100% solids therefore has low odor, no flammability, and is self-leveling.
APPLICATION TEMPERATURE: 55-90 degrees. FINISH CHARACTERISTICS: Gloss (70-95 at 60 degrees @ Erichsen glossmeter) 1.5 Gallon (175+ sq/ft) TENSILE STRENGTH: 4,800 psi @ ASTM D638 full cure (heavy traffic): 2-7 days @ 70 degrees F, APPLICATION TEMPERATURE: 60-90 degrees F with relative humidity below 85%, SOLIDS BY WEIGHT: 100% (+/- 1%) RECOMMENDED FILM THICKNESS: 12-30 mils recoat or topcoat: 8-12 hours @ 70 degrees F All dirt, foreign contaminants, oil and laitance must be removed to assure a trouble free bond to the substrate. Tack free (dry to touch): 6-8 hours @ 70 degrees F
HARDNESS: Shore D = 81 ABRASION RESISTANCE: Taber abraser CS-17 calibrase wheel with 1000 gram total load and 500 cycles = 36 mg loss If you are interested in a this kind of finish, check out our metallic epoxy floor kit page that includes complete kits and application instructions.
We recommend topcoating with a urethane product to assist in UV-resistance. Then broadcast aggregate into the coating while wet. tack free (dry to touch): 5-8 hours @ 70 degrees F This is a product guide to help you decide which epoxy is best for you. Norklad 100-UV is a two component 100% solids epoxy broadcast coat that can be filled withdecorativechips and colored sand mixtures to provide an infinite array of color schemes or patterns. HARDNESS: Shore D = 80. When to use Norklad 100-M: 100% solids is recommended for warehouses, kitchens, restrooms, and other areas where either a high build clear product is needed or where a decorative filled floor is desired. Full cure (heavy traffic): 2-7 days @ 70 degrees F It has a very fast pot life (30 minutes) once it's mixed with the converter.
If a blush is present, it must be removed prior to topcoating or recoating. SOLIDS BY VOLUME: 100% (+/- 1%) After mixing, transfer the mixed material to another pail (the transfer pail) and again remix. We highly recommend that the kits not be broken down unless suitable weighing equipment is available. Slip Resistant Floor Coating Grit Additives.
RECOMMENDED FILM THICKNESS: 16-18 mils
COVERAGE PER GALLON: 90-100 square feet per gallon @ 16-18 mils Always remember that colder temperatures will require more cure time for the product before recoating or topcoating can commence. If after 24 hours, the substrate is still dry below the plastic sheet, then the substrate is dry enough to start coating. RESTRICTIONS: Restrict the use of the floor to light traffic and non-harsh chemicals until the coating is fully cured (see technical data under full cure). If concrete conditions or over aggressive mixing causes air entrapment, then an air release roller tool should be used prior to the coating tacking off. The plastic sheet testing is also a good method to determine if any hydrostatic pressure problems exist that may later cause disbonding. A test should be made to determine that the concrete is dry; this can be done by placing a 4'x4' plastic sheet on the substrate and taping down the edges. COMPRESSIVE STRENGTH: 11,200 psi @ ASTM D695 If used alone, it is recommended that a primer coat be used to prevent outgassing/blistering. Low odor, low VOC formula is ideal for use on interior coated or bare concrete surfaces including garages, basements, workshops and more, Your email address will not be published. This website uses cookies to improve your experience while you navigate through the website. Apply your basecoat and colorchips and allow to sufficiently cure. ABRASION RESISTANCE: Taber abraser CS-17 calibrase wheel with 1000 gram total load and 500 cycles = 32 mg loss TOPCOAT: Urethane topcoat is recommended for added UV-Resistance if exposed to sunlight. If you are ready to purchase, head to our webstore. If a blush is present, it can be removed by any standard detergent cleaner prior to topcoating or recoating. We also use third-party cookies that help us analyze and understand how you use this website. Norklad 100 can easily coat over any solvent or water based epoxies. CLEANUP: Use xylol xylene. This category only includes cookies that ensures basic functionalities and security features of the website. It is 100% solids therefore has low odor, no flammability, and is self-leveling. COLOR: Clear PRODUCT APPLICATION: The mixed material can be applied by brush, roller or a serrated squeegee and then back rolled as long as the appropriate thickness recommendations are maintained. All dirt, foreign contaminants, oil and laitance must be removed to assure a trouble free bond to the substrate. (wait until you can no longer leave an imprint of your finger in the coating. This drawback of 100% solids epoxy can also be a positive; many professionals appreciate the fast potlife of 100% solids because it makes jobs faster and more efficient. A test should be made to determine that the concrete is dry; this can be done by placing a 4'x4' plastic sheet on the substrate and taping down the edges. It is mandatory to procure user consent prior to running these cookies on your website. PRODUCT APPLICATION: The mixed material can be applied by brush or roller. 100% solids is the industry standard for high-end commercial epoxy flooring. Norklad 200 is a two component 100% solids epoxy colored coating designed for applications where a high build colorfast impact resistant floor is needed. VISCOSITY: Mixed = 700-1000 cps (typical) A test should be made to determine that the concrete is dry; this can be done by placing a 4X4 plastic sheet on the substrate and taping down the edges. Any cookies that may not be particularly necessary for the website to function and is used specifically to collect user personal data via analytics, ads, other embedded contents are termed as non-necessary cookies. PRODUCT MIXING: This product has a mix ratio of 12# part A to 4.15# part B or two parts A to one part B by volume for standard colors. Orders placed over the next few months may be delayed or will be refunded. Best of all, they are abrasian resistant, chemical resistant, stain resistant, and all-around the most durable floor coating there is, by far.
RECOAT OR TOPCOATING: If you opt to recoat or topcoat this product, you must first be sure that the coating has tacked off before recoating. VOLATILE ORGANIC CONTENT: Nearly zero pounds per gallon If after 24 hours, the substrate is still dry below the plastic sheet, then the substrate is dry enough to start coating. Standard packages are packaged in 1.5-gal kits. RECOMMENDED FILM THICKNESS: 16-18 mils They are in pre-measured kits and should be mixed as supplied in the kit. Apply your base coat and colorchips and allow to sufficiently cure. These cookies will be stored in your browser only with your consent. After mixing, transfer the mixed material to another pail (the transfer pail) and again remix. COMPRESSIVE STRENGTH: 9,100 psi @ ASTM D695 1/2" X 1/2" bars 100% solids is the industry standard for high-end commercial epoxy flooring. The material in the transfer pail is now ready to be applied onto your base coat. See the front side of this technical data for primer information.
RECOAT OR TOPCOATING: If you opt to recoat or topcoat this product, you must first be sure that the coating has tacked off before recoating. Before recoating or topcoating, check the coating to insure no epoxy blushes were developed (a whitish, greasy film or deglossing). PRODUCT MIXING: This product has a mix ratio of 9.0# part A to 4.15# part B. All rights reserved | Privacy Policy | Terms of Use. MIX RATIO: 12 pounds (1 gallon) part A to 4.15 pounds (.50 gallons) part B (volumes approx.) When applied at 100 sq/ft per gallon, Norklad 100-UV willself-levelto a glasslike surface. 100% solids epoxy is the only epoxy that can be used for metallic epoxy floors (pictured above). SOLIDS BY WEIGHT: 100% You also have the option to opt-out of these cookies. *For best results, apply with a nap roller and/or squeegee. Some of our DIY customers have had great success by carefully researching and buying the proper tools, but know that if you have never installed a 100% epoxy floor before, you are taking a risk by doing so. Continuous storage should be between 60 and 90 degree F. Low temperatures or temperature fluctuations may cause product crystallization. i. After the two parts are combined, mix well with slow speed mixing equipment such as a jiffy mixer until the material is thoroughly mixed and streak free. COVERAGE PER GALLON: 90-100 square feet per gallon @ 16-18 mils Recoat or topcoat: 10-16 hours @ 70 degrees F Then broadcast aggregate into the coating while wet. Many epoxy coatings and urethanes as well as multiple coats of this product are compatible for use as a topcoat. Ideal for full broadcast terrazzo or colorchip floors. (1 gal of part a (resin) and half gallon of part b (hardener). PRODUCT MIXING: This product has a mix ratio of 9.0# part A to 4.15# part B. MIX RATIO: 9.0 pounds part A (.99 gallons) to 4.15 pounds part B (.49 gallons) (volumes approx.) PRIMING: A suitable primer should be used before applying this product.
If a primer is not used, more porous substrates may cause outgassing and possible surface defects. CURE SCHEDULE: This product can be used with random chip broadcasts, full chip broadcasts, or colored quartz.
GARDNER VARIABLE IMPACTOR: 50 inch pounds direct passed ABRASION RESISTANCE: Taber abraser CS-17 calibrase wheel with 1000 gram total load and 500 cycles = 36 mg loss
COMPRESSIVE STRENGTH: 11,200 psi @ ASTM D695 After the two parts are combined, mix well with slow speed mixing equipment such as a jiffy mixer until the material is thoroughly mixed and streak free. 100% solids epoxy does not have water or solvents that evaporate while curing; it retains 100% of its thickness and body after cure. The material in the transfer pail is now ready to be applied on the primed substrate.
ULTIMATE ELONGATION: 3.1% SOLIDS BY WEIGHT: 100% (wait until you can no longer leave an imprint of your finger in the coating.) VISCOSITY: Mixed = 700-1000 cps (typical) SOLIDS BY VOLUME: 100% VOLATILE ORGANIC CONTENT: Zero pounds per gallon We recommend topcoating with a urethane product to assist in UV-resistance.
APPLICATION TEMPERATURE: 55-90 degrees. FINISH CHARACTERISTICS: Gloss (70-95 at 60 degrees @ Erichsen glossmeter) 1.5 Gallon (175+ sq/ft) TENSILE STRENGTH: 4,800 psi @ ASTM D638 full cure (heavy traffic): 2-7 days @ 70 degrees F, APPLICATION TEMPERATURE: 60-90 degrees F with relative humidity below 85%, SOLIDS BY WEIGHT: 100% (+/- 1%) RECOMMENDED FILM THICKNESS: 12-30 mils recoat or topcoat: 8-12 hours @ 70 degrees F All dirt, foreign contaminants, oil and laitance must be removed to assure a trouble free bond to the substrate. Tack free (dry to touch): 6-8 hours @ 70 degrees F
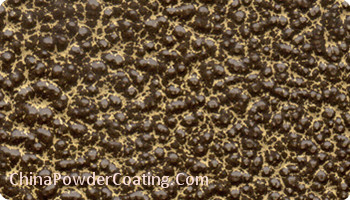
We recommend topcoating with a urethane product to assist in UV-resistance. Then broadcast aggregate into the coating while wet. tack free (dry to touch): 5-8 hours @ 70 degrees F This is a product guide to help you decide which epoxy is best for you. Norklad 100-UV is a two component 100% solids epoxy broadcast coat that can be filled withdecorativechips and colored sand mixtures to provide an infinite array of color schemes or patterns. HARDNESS: Shore D = 80. When to use Norklad 100-M: 100% solids is recommended for warehouses, kitchens, restrooms, and other areas where either a high build clear product is needed or where a decorative filled floor is desired. Full cure (heavy traffic): 2-7 days @ 70 degrees F It has a very fast pot life (30 minutes) once it's mixed with the converter.
If a blush is present, it must be removed prior to topcoating or recoating. SOLIDS BY VOLUME: 100% (+/- 1%) After mixing, transfer the mixed material to another pail (the transfer pail) and again remix. We highly recommend that the kits not be broken down unless suitable weighing equipment is available. Slip Resistant Floor Coating Grit Additives.
RECOMMENDED FILM THICKNESS: 16-18 mils
COVERAGE PER GALLON: 90-100 square feet per gallon @ 16-18 mils Always remember that colder temperatures will require more cure time for the product before recoating or topcoating can commence. If after 24 hours, the substrate is still dry below the plastic sheet, then the substrate is dry enough to start coating. RESTRICTIONS: Restrict the use of the floor to light traffic and non-harsh chemicals until the coating is fully cured (see technical data under full cure). If concrete conditions or over aggressive mixing causes air entrapment, then an air release roller tool should be used prior to the coating tacking off. The plastic sheet testing is also a good method to determine if any hydrostatic pressure problems exist that may later cause disbonding. A test should be made to determine that the concrete is dry; this can be done by placing a 4'x4' plastic sheet on the substrate and taping down the edges. COMPRESSIVE STRENGTH: 11,200 psi @ ASTM D695 If used alone, it is recommended that a primer coat be used to prevent outgassing/blistering. Low odor, low VOC formula is ideal for use on interior coated or bare concrete surfaces including garages, basements, workshops and more, Your email address will not be published. This website uses cookies to improve your experience while you navigate through the website. Apply your basecoat and colorchips and allow to sufficiently cure. ABRASION RESISTANCE: Taber abraser CS-17 calibrase wheel with 1000 gram total load and 500 cycles = 32 mg loss TOPCOAT: Urethane topcoat is recommended for added UV-Resistance if exposed to sunlight. If you are ready to purchase, head to our webstore. If a blush is present, it can be removed by any standard detergent cleaner prior to topcoating or recoating. We also use third-party cookies that help us analyze and understand how you use this website. Norklad 100 can easily coat over any solvent or water based epoxies. CLEANUP: Use xylol xylene. This category only includes cookies that ensures basic functionalities and security features of the website. It is 100% solids therefore has low odor, no flammability, and is self-leveling. COLOR: Clear PRODUCT APPLICATION: The mixed material can be applied by brush, roller or a serrated squeegee and then back rolled as long as the appropriate thickness recommendations are maintained. All dirt, foreign contaminants, oil and laitance must be removed to assure a trouble free bond to the substrate. (wait until you can no longer leave an imprint of your finger in the coating. This drawback of 100% solids epoxy can also be a positive; many professionals appreciate the fast potlife of 100% solids because it makes jobs faster and more efficient. A test should be made to determine that the concrete is dry; this can be done by placing a 4'x4' plastic sheet on the substrate and taping down the edges. It is mandatory to procure user consent prior to running these cookies on your website. PRODUCT APPLICATION: The mixed material can be applied by brush or roller. 100% solids is the industry standard for high-end commercial epoxy flooring. Norklad 200 is a two component 100% solids epoxy colored coating designed for applications where a high build colorfast impact resistant floor is needed. VISCOSITY: Mixed = 700-1000 cps (typical) A test should be made to determine that the concrete is dry; this can be done by placing a 4X4 plastic sheet on the substrate and taping down the edges. Any cookies that may not be particularly necessary for the website to function and is used specifically to collect user personal data via analytics, ads, other embedded contents are termed as non-necessary cookies. PRODUCT MIXING: This product has a mix ratio of 12# part A to 4.15# part B or two parts A to one part B by volume for standard colors. Orders placed over the next few months may be delayed or will be refunded. Best of all, they are abrasian resistant, chemical resistant, stain resistant, and all-around the most durable floor coating there is, by far.
RECOAT OR TOPCOATING: If you opt to recoat or topcoat this product, you must first be sure that the coating has tacked off before recoating. VOLATILE ORGANIC CONTENT: Nearly zero pounds per gallon If after 24 hours, the substrate is still dry below the plastic sheet, then the substrate is dry enough to start coating. Standard packages are packaged in 1.5-gal kits. RECOMMENDED FILM THICKNESS: 16-18 mils They are in pre-measured kits and should be mixed as supplied in the kit. Apply your base coat and colorchips and allow to sufficiently cure. These cookies will be stored in your browser only with your consent. After mixing, transfer the mixed material to another pail (the transfer pail) and again remix. COMPRESSIVE STRENGTH: 9,100 psi @ ASTM D695 1/2" X 1/2" bars 100% solids is the industry standard for high-end commercial epoxy flooring. The material in the transfer pail is now ready to be applied onto your base coat. See the front side of this technical data for primer information.
RECOAT OR TOPCOATING: If you opt to recoat or topcoat this product, you must first be sure that the coating has tacked off before recoating. Before recoating or topcoating, check the coating to insure no epoxy blushes were developed (a whitish, greasy film or deglossing). PRODUCT MIXING: This product has a mix ratio of 9.0# part A to 4.15# part B. All rights reserved | Privacy Policy | Terms of Use. MIX RATIO: 12 pounds (1 gallon) part A to 4.15 pounds (.50 gallons) part B (volumes approx.) When applied at 100 sq/ft per gallon, Norklad 100-UV willself-levelto a glasslike surface. 100% solids epoxy is the only epoxy that can be used for metallic epoxy floors (pictured above). SOLIDS BY WEIGHT: 100% You also have the option to opt-out of these cookies. *For best results, apply with a nap roller and/or squeegee. Some of our DIY customers have had great success by carefully researching and buying the proper tools, but know that if you have never installed a 100% epoxy floor before, you are taking a risk by doing so. Continuous storage should be between 60 and 90 degree F. Low temperatures or temperature fluctuations may cause product crystallization. i. After the two parts are combined, mix well with slow speed mixing equipment such as a jiffy mixer until the material is thoroughly mixed and streak free. COVERAGE PER GALLON: 90-100 square feet per gallon @ 16-18 mils Recoat or topcoat: 10-16 hours @ 70 degrees F Then broadcast aggregate into the coating while wet. Many epoxy coatings and urethanes as well as multiple coats of this product are compatible for use as a topcoat. Ideal for full broadcast terrazzo or colorchip floors. (1 gal of part a (resin) and half gallon of part b (hardener). PRODUCT MIXING: This product has a mix ratio of 9.0# part A to 4.15# part B. MIX RATIO: 9.0 pounds part A (.99 gallons) to 4.15 pounds part B (.49 gallons) (volumes approx.) PRIMING: A suitable primer should be used before applying this product.
If a primer is not used, more porous substrates may cause outgassing and possible surface defects. CURE SCHEDULE: This product can be used with random chip broadcasts, full chip broadcasts, or colored quartz.
GARDNER VARIABLE IMPACTOR: 50 inch pounds direct passed ABRASION RESISTANCE: Taber abraser CS-17 calibrase wheel with 1000 gram total load and 500 cycles = 36 mg loss
COMPRESSIVE STRENGTH: 11,200 psi @ ASTM D695 After the two parts are combined, mix well with slow speed mixing equipment such as a jiffy mixer until the material is thoroughly mixed and streak free. 100% solids epoxy does not have water or solvents that evaporate while curing; it retains 100% of its thickness and body after cure. The material in the transfer pail is now ready to be applied on the primed substrate.
ULTIMATE ELONGATION: 3.1% SOLIDS BY WEIGHT: 100% (wait until you can no longer leave an imprint of your finger in the coating.) VISCOSITY: Mixed = 700-1000 cps (typical) SOLIDS BY VOLUME: 100% VOLATILE ORGANIC CONTENT: Zero pounds per gallon We recommend topcoating with a urethane product to assist in UV-resistance.