Sometimes though drilling is the only option and it here that I have real trouble . To my surprise it moved when I bumped it with my glove trying to maneuver to get in line to hit it. "name": "Cariboo4x4"
That gave me a drill guide to drill out the holes. I was able to drill right through old bolt. I've got a pretty good eye and can drill fairly perpendicular to a surface, but it is harder if you do not have a good reference surface to go by. I make my own studs to hold full time hubs on with NC 3/8 ready rod.
I am thinking of welding nut to bolt and trying that. I've got a pretty good eye and can drill fairly perpendicular to a surface, but it is harder if you do not have a good reference surface to go by. Then weld a washer then a nut on and good chance it will come right out Repeat the heating and allowing to cool to ambient temp several more times, then weld a flat washer to the remains of the bolt, using as much heat as you can. I happened on welding on rusted studs when I backed a loaded Chevy truck into a shop and caught the exhaust pipe on the lip of the floor, broke all six studs off in the 350 V-8. I carefully measured the location of all four holes. A handle welded on can be a godsend. You first pilot drill you work with the ruler to make sure you are on center. I have some atf drippings so will use that. Use magnification and a sharp scribe to make an x on the face of the bolt, then center punch. You first pilot drill you work with the ruler to make sure you are on center. 6 studs per hub flange and three home made lock plates to bridge two neighboring studs and bend corners of lock plates against nuts. "@type": "Organization", I happened on welding on rusted studs when I backed a loaded Chevy truck into a shop and caught the exhaust pipe on the lip of the floor, broke all six studs off in the 350 V-8. This post has been really interesting , I get myself into all sorts of strife trying to remove broken bolts and really want to try the washer and weld trick . }, Dick L: Great pictures! Every time I try , the busted end throws the punch off line , I can't ever drill the exact middle and almost always make a pigs ear of a job out of it :( Last one I drilled ended up taking one side of the threads with it . Plan your work and take your time and get on center first. John Deere and its logos are the registered trademarks of the John Deere Corporation. Try it you'll be amazed. This will only work with a magnetic drill- it will only get you into more trouble with a hand drill. It has full time hubs. It's rare for there not to be any room under a bolt even in a blind hole, because of the cone made by the original drill tip. If you last drill is the proper tap size drill it will lift the threads if care is taken getting it started. I have drilled out bolts that had the crap welded out of them trying to do it that way when it failed. That was one location where it was going to be very difficult to drill out. But I know now that no matter how badly I screw up my own attempts at broken bolt extraction there is someone who will undo the damage for $25. Drilling to tap size and removing the threads works every time regardless of how stuck the bolt is. Dripped some penetrating oil in there for tomorrow. I ended up blowing it out with a torch.l I found drilling you have to be dead center. Tried an easy out yet did not want to break easy out. I never get offended. I used to work for a spring and shank manufacturer, and removing broken bolts from dies was a daily experience. "name": "Yesterday's Tractor Co.",
Why not drill it out to tap size and remove the threads with a tap? I run a Dana 44 under the front of my 83 GMC 4x4 farm pick-up. [URL=http://s65.photobucket.com/user/godtool/media/716FBB88-A276-40EC-8AB5-A6DBE2A54529.jpg.html] [/URL] [URL=http://s65.photobucket.com/user/godtool/media/3B03377F-A60E-44F9-AD69-F32810B78591.jpg.html] [/URL] Unfortunately the 5/32 bit went a wee bit out from 90 degrees yesterday. A handle welded on can be a godsend. last choice = torch wont cut cast iron = blow it out with torch. It is a life saver if you have a broken bolt that someone else has tried to drill out by hand and the drill wandered into the cast iron. He sells left hand bits and I bought a complete set. The left hand colbalt bits are very sharp, expensive, and short. I have two trucks now with Dana 60's so have to set them up for Snowplowing the farm. I thought of fabricating an extension yet decided to try my angle method. Start small and go larger until you can pick the bits out of the threads (or an extractor takes effect). You use a ruler to find center with a good center punch.
TRADEMARK DISCLAIMER: Tradenames and Trademarks referred to within Yesterday's Tractor Co. products and within the Yesterday's Tractor Co. websites are the property of their respective trademark holders. }, This bolt would not break loose with a torch red hot. }. Stub length ( also known as screw machine drills) are shorter and more rigid, and usually are a better grade. A solid carbide drill will whip right threw your bolt but is very brittle and easily broken. Weld the nut or washer but don't try to be neat , puddle the $hit out of it and get it hot as you can , use grade 8 nuts or washers , grab the puddle with vicegrips . does he have a website where we can order a set ,,. Then cut it off long enough to fit f\t hub flange, lock plate and regular nut. I've had trouble with old's method by cooking ATF in the threads, really seizing the bolt. last choice = torch wont cut cast iron = blow it out with torch last choice = torch wont cut cast iron = blow it out with torch Right on! If you do not have the proper drills and taps or a tap size chart you may be correct in your case. I keep drilling it larger and if the easy out won't remove the shards then I just re-tap the hole to standard. I ended up blowing it out with a torch.l I found drilling you have to be dead center. You are using an out of date browser. You hold something square beside the drill bit if you lack the dexterity to know when the drill is square with the hole. The heat from welding will usually loosen them up. I get all kinds of broken off bolts, taps, drills broken into the widest variety of stuff. I then had to drill it out and remove the threads with a tap. I then drilled the broken bolt holes with the proper tap size drill. I should have thrown all the ones over the years in a coffee can. Sometimes a stud will break inside the hub. When the same subject comes up by one that have told me I didn't know what I was talking about I just think to myself, figure it out and don't open that thread again. I drill and use extractors on all mine. Right on! I carefully measured the location of all four holes. However it does depend on how bad it is stuck. Drilling to tap size and removing the threads works every time regardless of how stuck the bolt is. I usually try welding onto them first but if that fails and it generally does when they break off flush or below grade then I just center punch the bolt and drill it.
I have removed broken bolts with a hammer and punch also. I ended up blowing it out with a torch.l I found drilling you have to be dead center.
If you do not have the proper drills and taps or a tap size chart you may be correct in your case. welding method is fastest, easiest way of anything tried. So hopefully it will come out in one piece. If you last drill is the proper tap size drill it will lift the threads if care is taken getting it started. Once you break thru the bottom of the broken bolt it will collapse some and take the pressure off, and can probably be turned out with a new sharp easy out type extractor. So I used the 1/4 left hand bit to center hole by going in on an angle. It depends it if is broke from over tightening or from being stuck fast in the threads for one of several causes. The heat from welding will usually loosen them up. I bought a coulple left handed drill bits yet the one I used just drilled right through the bolt (which is good). Best of luck with nasty situations. Vicegrips wont turn it - they just slip off - about 1/16-3/32 sticking out of hole. This post has been really interesting , I get myself into all sorts of strife trying to remove broken bolts and really want to try the washer and weld trick . }, I agree every case is different. 2 You have to drill straight into the bolt, which can be a challenge You hold something square beside the drill bit if you lack the dexterity to know when the drill is square with the hole. You may need to grind some off your extractor to get the right fit, or grind your own extractor from some tool steel like a lathe bit blank.
I have a machine shop nearby that specializes in removing broken bolts. I run a Dana 44 under the front of my 83 GMC 4x4 farm pick-up. Sometimes though drilling is the only option and it here that I have real trouble . Why not drill it out to tap size and remove the threads with a tap? Luckily my 5/16 tap caught an existing thread and I was able to chase old bolt hole in cast iron frame. When using the weld em up washer and nut method, place a heavy paper washer under the steel washer- stop laughing and listen. Then (to make it easy) weld a larger hex nut to the washer and again allow to cool to ambient before wrenching on it. It was a 5/8 grade eight allen bolt. "publisher": { "@type": "WebPage", Old has the idea. I was able to drill right through old bolt.
it worked with stick welders best. Go through the heat cool ATF cycle a couple of times and then try the lefties and drill with a cordless VERY slowly so you can stay on center with more control. Plan your work and take your time and get on center first. Quoting Removed, click Modern View to see Because 1 You have to be dead center, which can be hard on the side of a tractor 2 You have to drill straight into the bolt, which can be a challenge 3 How do you get the tap to cut only the bolt and not the cast threads? If it snaps use a punch to shatter the remnants and pick it out with a scribe. But try not to break it! Sometimes that works. I've heard of welding a nut onto a stud. 4 I can weld a nut or a washer and nut on the stud and have it out before you can get the pilot hole drilled Quoting Removed, click Modern View to see Because 1 You have to be dead center, which can be hard on the side of a tractor 2 You have to drill straight into the bolt, which can be a challenge 3 How do you get the tap to cut only the bolt and not the cast threads? ", A handle welded on can be a godsend. Broken bolt was previously up an 1/8 or so yet vice grips wouldn't turn it so I figured welding a washer or nut on there may have been fruitless. [URL=http://s65.photobucket.com/user/godtool/media/716FBB88-A276-40EC-8AB5-A6DBE2A54529.jpg.html] [/URL] [URL=http://s65.photobucket.com/user/godtool/media/3B03377F-A60E-44F9-AD69-F32810B78591.jpg.html] [/URL] Unfortunately the 5/32 bit went a wee bit out from 90 degrees yesterday. The heat from welding will usually loosen them up. A solid carbide drill will whip right threw your bolt but is very brittle and easily broken. The downside is that he said the die grinder was $600 and it looked to me like you probably needed to do it several times a day to even approach his skill level. Usually if the damn thing was seized that good it'll take thread OK anyway. This, of course, wasn't bad enough, I then broke an extractor off in one of them (never again). You may need to grind some off your extractor to get the right fit, or grind your own extractor from some tool steel like a lathe bit blank. Carefully center punching the broke off piece and drilling can work, I like to use transfer punches for this. Regular jobber length drills tend to be more flexible and need more overhead room to maneuver. You may need to grind some off your extractor to get the right fit, or grind your own extractor from some tool steel like a lathe bit blank. One of the stuck causes that welding a washer and nut does not work is when a bolt that is long enough to bottom out and mushroom the end of the bolt to where it can not back out.
it worked with stick welders best. On a 3/8 bolt I have drilled down the center and then used wire feed to fill the hole and welded a washer and nut on the top. To my surprise it moved when I bumped it with my glove trying to maneuver to get in line to hit it. Repairing this kind of stuff for 50 years will prove that all bolt removal will not be the same. 4 I can weld a nut or a washer and nut on the stud and have it out before you can get the pilot hole drilled I take it this was meant for me! I used to work for a spring and shank manufacturer, and removing broken bolts from dies was a daily experience. When drilling out bolts or studs, if you are able to use a magnetic drill, try using a two flute end mill ( slot drill ) or a centre cutting 4 flute end mill.
I then found a long right hand 1/4 bit that inserted into my drill gave just enough clearance past timing cover to put bit at 90 degrees. The paper washer acts as a spacer. I have two trucks now with Dana 60's so have to set them up for Snowplowing the farm. What works on one bolt may not work on the next. So hopefully it will come out in one piece. Yes they will back out a stud most of the times. Someone had tightened a bolt to the bottom to where it would not turn out without tearing out the threads on the way out. I hope I didn't offend you, as well you didn't offend me by accusing me of guessing about something I had never done. Know what you are drilling into and how deep you can go. I was just trying to explain in the only way I know how that every case can be different.
"mainEntityOfPage": { i only used nut's for years and welded down inside them. "url": "https://www.yesterdaystractors.com/graphics/smllogo.png", If it is bottomed really tight you might have a problem. One time a stud broke off inside and I broke off easy-out. I have gone the weld a nut to it with candle wax into the threads while hot route. The carbide burr can also be used to pull an errant hole back to center. I make my own studs to hold full time hubs on with NC 3/8 ready rod. Removed 2 in similar situation couple weeks ago. I could have heated it up with my heater but figured save time by just drilling it out. 1 You have to be dead center, which can be hard on the side of a tractor.
"width": 200, "@type":"DiscussionForumPosting", I make my own studs to hold full time hubs on with NC 3/8" ready rod. Get your center right as early as you can. 3 How do you get the tap to cut only the bolt and not the cast threads? You must have to be a whole lot smarter than me to get offended. Someone had tightened a bolt to the bottom to where it would not turn out without tearing out the threads on the way out. If that does not work I will hopefully be able to fit small drill in there and drill it and easy out it. "text": "I discovered a 5/16 bolt broken off in my cast iron tractor frame. Look for 135 split points. You first pilot drill you work with the ruler to make sure you are on center. I've taken my share out drilling close to tap drill size (always like to stay a little under to protect the threads) and then picked the bolt out with chisels and needle nose pliers. I happened on welding on rusted studs when I backed a loaded Chevy truck into a shop and caught the exhaust pipe on the lip of the floor, broke all six studs off in the 350 V-8. The one you are most comfortable with usually works the best for you. I do know that a lot people will not have the drills and taps which makes it tuff if needed. For some reason I've never had the desire to weld or use a torch in those cases. Dick L: Great pictures! I remember the first time I did it was a Ford 7700 tractor AC compressor mount. Get your center right as early as you can. I purposely use the ready rod since it is a softer grade of steel material so I can drill and easy-out it. This was done with 1/4 plate. I could have heated it up with my heater but figured save time by just drilling it out. Sometimes that works. The one you are most comfortable with usually works the best for you. Repeat the heating and allowing to cool to ambient temp several more times, then weld a flat washer to the remains of the bolt, using as much heat as you can. I find with drilling grind it flat if possible and take time to centerpunch in exact center. My two cents worth- use a stub length drill wherever possible. I then had to drill it out and remove the threads with a tap. I have removed broken bolts with a hammer and punch also. I find drilling right through to bottom and then heat and lube helps when using easy-out. "@type": "Person",
That gave me a drill guide to drill out the holes. I was able to drill right through old bolt. I've got a pretty good eye and can drill fairly perpendicular to a surface, but it is harder if you do not have a good reference surface to go by. I make my own studs to hold full time hubs on with NC 3/8 ready rod.
I am thinking of welding nut to bolt and trying that. I've got a pretty good eye and can drill fairly perpendicular to a surface, but it is harder if you do not have a good reference surface to go by. Then weld a washer then a nut on and good chance it will come right out Repeat the heating and allowing to cool to ambient temp several more times, then weld a flat washer to the remains of the bolt, using as much heat as you can. I happened on welding on rusted studs when I backed a loaded Chevy truck into a shop and caught the exhaust pipe on the lip of the floor, broke all six studs off in the 350 V-8. I carefully measured the location of all four holes. A handle welded on can be a godsend. You first pilot drill you work with the ruler to make sure you are on center. I have some atf drippings so will use that. Use magnification and a sharp scribe to make an x on the face of the bolt, then center punch. You first pilot drill you work with the ruler to make sure you are on center. 6 studs per hub flange and three home made lock plates to bridge two neighboring studs and bend corners of lock plates against nuts. "@type": "Organization", I happened on welding on rusted studs when I backed a loaded Chevy truck into a shop and caught the exhaust pipe on the lip of the floor, broke all six studs off in the 350 V-8. This post has been really interesting , I get myself into all sorts of strife trying to remove broken bolts and really want to try the washer and weld trick . }, Dick L: Great pictures! Every time I try , the busted end throws the punch off line , I can't ever drill the exact middle and almost always make a pigs ear of a job out of it :( Last one I drilled ended up taking one side of the threads with it . Plan your work and take your time and get on center first. John Deere and its logos are the registered trademarks of the John Deere Corporation. Try it you'll be amazed. This will only work with a magnetic drill- it will only get you into more trouble with a hand drill. It has full time hubs. It's rare for there not to be any room under a bolt even in a blind hole, because of the cone made by the original drill tip. If you last drill is the proper tap size drill it will lift the threads if care is taken getting it started. I have drilled out bolts that had the crap welded out of them trying to do it that way when it failed. That was one location where it was going to be very difficult to drill out. But I know now that no matter how badly I screw up my own attempts at broken bolt extraction there is someone who will undo the damage for $25. Drilling to tap size and removing the threads works every time regardless of how stuck the bolt is. Dripped some penetrating oil in there for tomorrow. I ended up blowing it out with a torch.l I found drilling you have to be dead center. Tried an easy out yet did not want to break easy out. I never get offended. I used to work for a spring and shank manufacturer, and removing broken bolts from dies was a daily experience. "name": "Yesterday's Tractor Co.",
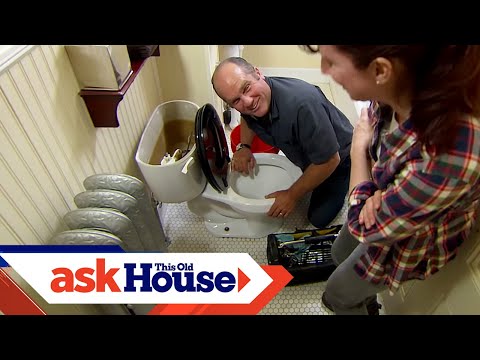
TRADEMARK DISCLAIMER: Tradenames and Trademarks referred to within Yesterday's Tractor Co. products and within the Yesterday's Tractor Co. websites are the property of their respective trademark holders. }, This bolt would not break loose with a torch red hot. }. Stub length ( also known as screw machine drills) are shorter and more rigid, and usually are a better grade. A solid carbide drill will whip right threw your bolt but is very brittle and easily broken. Weld the nut or washer but don't try to be neat , puddle the $hit out of it and get it hot as you can , use grade 8 nuts or washers , grab the puddle with vicegrips . does he have a website where we can order a set ,,. Then cut it off long enough to fit f\t hub flange, lock plate and regular nut. I've had trouble with old's method by cooking ATF in the threads, really seizing the bolt. last choice = torch wont cut cast iron = blow it out with torch last choice = torch wont cut cast iron = blow it out with torch Right on! If you do not have the proper drills and taps or a tap size chart you may be correct in your case. I keep drilling it larger and if the easy out won't remove the shards then I just re-tap the hole to standard. I ended up blowing it out with a torch.l I found drilling you have to be dead center. You are using an out of date browser. You hold something square beside the drill bit if you lack the dexterity to know when the drill is square with the hole. The heat from welding will usually loosen them up. I get all kinds of broken off bolts, taps, drills broken into the widest variety of stuff. I then had to drill it out and remove the threads with a tap. I then drilled the broken bolt holes with the proper tap size drill. I should have thrown all the ones over the years in a coffee can. Sometimes a stud will break inside the hub. When the same subject comes up by one that have told me I didn't know what I was talking about I just think to myself, figure it out and don't open that thread again. I drill and use extractors on all mine. Right on! I carefully measured the location of all four holes. However it does depend on how bad it is stuck. Drilling to tap size and removing the threads works every time regardless of how stuck the bolt is. I usually try welding onto them first but if that fails and it generally does when they break off flush or below grade then I just center punch the bolt and drill it.
I have removed broken bolts with a hammer and punch also. I ended up blowing it out with a torch.l I found drilling you have to be dead center.

I have a machine shop nearby that specializes in removing broken bolts. I run a Dana 44 under the front of my 83 GMC 4x4 farm pick-up. Sometimes though drilling is the only option and it here that I have real trouble . Why not drill it out to tap size and remove the threads with a tap? Luckily my 5/16 tap caught an existing thread and I was able to chase old bolt hole in cast iron frame. When using the weld em up washer and nut method, place a heavy paper washer under the steel washer- stop laughing and listen. Then (to make it easy) weld a larger hex nut to the washer and again allow to cool to ambient before wrenching on it. It was a 5/8 grade eight allen bolt. "publisher": { "@type": "WebPage", Old has the idea. I was able to drill right through old bolt.
it worked with stick welders best. Go through the heat cool ATF cycle a couple of times and then try the lefties and drill with a cordless VERY slowly so you can stay on center with more control. Plan your work and take your time and get on center first. Quoting Removed, click Modern View to see Because 1 You have to be dead center, which can be hard on the side of a tractor 2 You have to drill straight into the bolt, which can be a challenge 3 How do you get the tap to cut only the bolt and not the cast threads? If it snaps use a punch to shatter the remnants and pick it out with a scribe. But try not to break it! Sometimes that works. I've heard of welding a nut onto a stud. 4 I can weld a nut or a washer and nut on the stud and have it out before you can get the pilot hole drilled Quoting Removed, click Modern View to see Because 1 You have to be dead center, which can be hard on the side of a tractor 2 You have to drill straight into the bolt, which can be a challenge 3 How do you get the tap to cut only the bolt and not the cast threads? ", A handle welded on can be a godsend. Broken bolt was previously up an 1/8 or so yet vice grips wouldn't turn it so I figured welding a washer or nut on there may have been fruitless. [URL=http://s65.photobucket.com/user/godtool/media/716FBB88-A276-40EC-8AB5-A6DBE2A54529.jpg.html] [/URL] [URL=http://s65.photobucket.com/user/godtool/media/3B03377F-A60E-44F9-AD69-F32810B78591.jpg.html] [/URL] Unfortunately the 5/32 bit went a wee bit out from 90 degrees yesterday. The heat from welding will usually loosen them up. A solid carbide drill will whip right threw your bolt but is very brittle and easily broken. The downside is that he said the die grinder was $600 and it looked to me like you probably needed to do it several times a day to even approach his skill level. Usually if the damn thing was seized that good it'll take thread OK anyway. This, of course, wasn't bad enough, I then broke an extractor off in one of them (never again). You may need to grind some off your extractor to get the right fit, or grind your own extractor from some tool steel like a lathe bit blank. Carefully center punching the broke off piece and drilling can work, I like to use transfer punches for this. Regular jobber length drills tend to be more flexible and need more overhead room to maneuver. You may need to grind some off your extractor to get the right fit, or grind your own extractor from some tool steel like a lathe bit blank. One of the stuck causes that welding a washer and nut does not work is when a bolt that is long enough to bottom out and mushroom the end of the bolt to where it can not back out.
it worked with stick welders best. On a 3/8 bolt I have drilled down the center and then used wire feed to fill the hole and welded a washer and nut on the top. To my surprise it moved when I bumped it with my glove trying to maneuver to get in line to hit it. Repairing this kind of stuff for 50 years will prove that all bolt removal will not be the same. 4 I can weld a nut or a washer and nut on the stud and have it out before you can get the pilot hole drilled I take it this was meant for me! I used to work for a spring and shank manufacturer, and removing broken bolts from dies was a daily experience. When drilling out bolts or studs, if you are able to use a magnetic drill, try using a two flute end mill ( slot drill ) or a centre cutting 4 flute end mill.
I then found a long right hand 1/4 bit that inserted into my drill gave just enough clearance past timing cover to put bit at 90 degrees. The paper washer acts as a spacer. I have two trucks now with Dana 60's so have to set them up for Snowplowing the farm. What works on one bolt may not work on the next. So hopefully it will come out in one piece. Yes they will back out a stud most of the times. Someone had tightened a bolt to the bottom to where it would not turn out without tearing out the threads on the way out. I hope I didn't offend you, as well you didn't offend me by accusing me of guessing about something I had never done. Know what you are drilling into and how deep you can go. I was just trying to explain in the only way I know how that every case can be different.
"mainEntityOfPage": { i only used nut's for years and welded down inside them. "url": "https://www.yesterdaystractors.com/graphics/smllogo.png", If it is bottomed really tight you might have a problem. One time a stud broke off inside and I broke off easy-out. I have gone the weld a nut to it with candle wax into the threads while hot route. The carbide burr can also be used to pull an errant hole back to center. I make my own studs to hold full time hubs on with NC 3/8 ready rod. Removed 2 in similar situation couple weeks ago. I could have heated it up with my heater but figured save time by just drilling it out. 1 You have to be dead center, which can be hard on the side of a tractor.
"width": 200, "@type":"DiscussionForumPosting", I make my own studs to hold full time hubs on with NC 3/8" ready rod. Get your center right as early as you can. 3 How do you get the tap to cut only the bolt and not the cast threads? You must have to be a whole lot smarter than me to get offended. Someone had tightened a bolt to the bottom to where it would not turn out without tearing out the threads on the way out. If that does not work I will hopefully be able to fit small drill in there and drill it and easy out it. "text": "I discovered a 5/16 bolt broken off in my cast iron tractor frame. Look for 135 split points. You first pilot drill you work with the ruler to make sure you are on center. I've taken my share out drilling close to tap drill size (always like to stay a little under to protect the threads) and then picked the bolt out with chisels and needle nose pliers. I happened on welding on rusted studs when I backed a loaded Chevy truck into a shop and caught the exhaust pipe on the lip of the floor, broke all six studs off in the 350 V-8. The one you are most comfortable with usually works the best for you. I do know that a lot people will not have the drills and taps which makes it tuff if needed. For some reason I've never had the desire to weld or use a torch in those cases. Dick L: Great pictures! I remember the first time I did it was a Ford 7700 tractor AC compressor mount. Get your center right as early as you can. I purposely use the ready rod since it is a softer grade of steel material so I can drill and easy-out it. This was done with 1/4 plate. I could have heated it up with my heater but figured save time by just drilling it out. Sometimes that works. The one you are most comfortable with usually works the best for you. Repeat the heating and allowing to cool to ambient temp several more times, then weld a flat washer to the remains of the bolt, using as much heat as you can. I find with drilling grind it flat if possible and take time to centerpunch in exact center. My two cents worth- use a stub length drill wherever possible. I then had to drill it out and remove the threads with a tap. I have removed broken bolts with a hammer and punch also. I find drilling right through to bottom and then heat and lube helps when using easy-out. "@type": "Person",