Their usage extends past manufacturing and industrial environments, and they are the driving device in the fuel level gauges in most airplanes, cars, and boats. The rise in the production of vehicles, the development of smaller, smarter, and cheaper sensors, and supportive government regulations are the major factors that are expected to be driving the industrial level sensors market. 1025 W 1700 N Logan, UT 84321Phone: (877) 373-5940Fax: (435) 753-7490 The ultrasonic sensor calculates the distance to the target based on the amount of the time that it took for the sound wave to return to the transmitter. Pros Solid-state, can be non-invasive, compact, accurate, Cons May require calibration, can only be used in certain liquids. Level sensors are devices that are used to measure the substances, such as water, oil, slurries, dust particles, solids, etc. These are very accurate and need no calibration. Anything that deflects or absorbs the signal, or acts as a false surface, may cause erroneous readings. Capacitance level sensors operate in the way that process fluids have dielectric constants, significantly different to air.
It can be used with different fluid densities, The measurement is possible if there is a large amount of liquid, It can be used to measure the level of water, oil, hydraulic fluids, and chemicals, It can be used for high temperature and pressure, Fluid density change would affect the measurement, Only non-corrosive liquids can be measured, It cant be used with dangerous process fluids, It can be operated in high temperature and pressure, It cant be used with varying dielectric materials, It cant be used with media that coats the sensing element, Measurement is affected by the variations in temperature, It can only be used with conductive liquids, It can be used with highly corrosive liquids, It can be used for solid and liquid level control, It can be used with media that exhibit sticky properties or foam, It is independent of the media characteristics, It cant be used for continuous level measurement, It is used to control the maximum amount of solids and liquids in many applications such as grains, cement, granules, powder, It can be used to do the level control of paste or adhesive media, It can be used to do the level measurement of small tanks, A specified amount of conductivity is required for the media, It can be used with sticky or foaming media, Measurement is not affected by the type of media which is to be measured, High pressure and temperature could affect the measurement, Reflections could happen due to agitation, Foam, steam, change in concentration would affect the measurement. Applications level control of liquid, powders and fine grained solids within mining, chemical processing and food and beverage industries. If you have to turn up your sensitivity too much, youll start to pick up unwanted echoes and erroneous readings.
In this level sensor, self-cleaning is required because of the vibrations they give off and is unaffected by the properties of the material they are sensing. Happy Reading! Several of our models are a good fit for this application. So from the source, electromagnetic radiation is transmitted and this radiation is emitted in a way that it would pass through the material to reach the transmitter which is placed on the opposite side of the tank.
It uses a probe to read conductivity.
Essentially, youre causing your sensor to double check the changes in the level before it serves it to you as an output. This type of industrial level sensor is one of the most cost-effective, but well-proven technologies for liquid level sensing. Ultrasonic sensors work on the basic principle of sound waves (mechanical energy) to determine material level. In addition, the sensor needs to be calibrated to the specific material to excuse the varying dielectric constants and differences in the tank design. Trip points help you control pumps, alarms, and valves easily. Our client success team member will get in touch with you shortly to take this ahead. Our ultrasonic level sensors are quite accurate (0.25% of detected range), and suitable for most measurements outside of custody transfer applications. This is similar to the float switch and it has a magnetic sleeve and this would be attached to the spring so when the spring moves the magnet would move along it and thus switching would be done.
Float switches are one of the most cost effective but also well proven technologies for water level sensing.
By using a high energy IR diode and pulse modulation methods, the interference from the produced light can be reduced.
This means that youll never know if their ultrasonic sensor will work for you. For large tanks and industrial applications In simple terms, they work by converting light rays into electrical signals which measure a physical quantity of light and then translate it into a measurement. So if you have your pulse strength ramped up as high as you can just to get a good return signal, it means your sensors isnt powerful enough. Liquid level sensors have been around for decades, in markets such as food and beverage, industrial, medical and domestic, printing, agriculture, automotive and white goods for leak detection or level measurement.We often wonder why customers choose one technology over the other and it is a common question we are asked. In this type of level measurement, the fluid conductivity is utilized to do the measurement.
Applications tank level measurement and leakdetection applications.
Optical liquid level switches are suitable for high, low or intermediate level detection in practically any tank, large or small. This type of sensor is used for single location measurement of the fluid. These sensors send microwaves by an antenna on the radar sensor.
However, cleaning is required if the lens gets dirty or coated. A more powerful sensor can also be used to strengthen the signal. Is the measured material electrically conductive?
Programming our ultrasonic level sensors is relatively easy, and is usually done well in under 30 minutes. Due to this the force that acts on the spring would vary and thus the spring would compress. This type of level measurement is done by transmitting gamma source and in order to do that cesium or cobalt isotope is used as the source. Typically, suppliers will offer a range of mounting options, with the most common being horizontal/side mounting and vertical mounting. Some equipment manufacturers may also be surprised at both the variety and intelligence of level sensing alternatives available on the market.
However, the tuning fork sensors can be used in conjunction with continuous level detection systems, acting as alarm points for leaks and over-filling. Pros No moving parts, compact, reliable, not affected by media properties, Cons expensive, invasive, performance can be affected by various elements in the environment, Applications Non contact applications with highly viscous and bulk solids. This type of level measurement is a continuous level measurement and a capacitance probe is used for this measurement. The radar sensors are unaffected by dust, temperature, or pressure. Most of our ultrasonic sensors are designed for use in level applications with ranges from as little as 4 inches to as much as 50 feet. Contact Madison Company if you have technical questions or need additional information not displayed here.
Advantages of the conductive level sensor, Disadvantages of the conductive level sensor, Applications of the conductive level sensor. However, with the competitive nature of the industry and the consistently wanting to improve quality, reduce costs, inefficiencies and waste kind of mentality, no company wants to take the risk at offering solutions that are not performing as best as they could be. The variation in the fluid level could be sensed by the level sensor and it would transmit this info to the operator. Does turbulence, surface foam, vapor, coating of sensors occur at the surface of the liquid? They are also utilized in systems in which temperatures differ. Ultrasonic sensors require an unobstructed air column between the sensor and the target. The trick is really to use an ultrasonic sensor with double the needed range. The industrial ultrasonic level sensors have no moving parts, are compact and cost-effective, reliable, and non-invasive. Open channels are a primary means of transporting, filtering, and metering water. In principle radar works in a similar way to ultrasonic, but the pulses travel at the speed of light and again; the reliability and repeatability can be affected but this time by the dielectric constant of the fluid. However, they may require calibration and can only be used in certain liquids. When the probes are in liquid, the current flows across both probes to activate the switch. One such technology is ultrasonic. Besides, the transducer is necessary to be increased appropriately to get a better response. This parameter would be calculated to determine the fluid level.
The long probe transmits a low voltage, the second shorter probe is cut so the tip is at the switching point. These sound waves then reflect off the liquid surface you are trying to measure. This glass tube will be connected to the tank at the bottom with proper fittings so that the pressure could be retained. In this type of level measurement, a buoyant object will be placed between the fluid which is to be measured and also the headspace vapor in the tank.
This type of sensor is used in multiple locations to do the level measurement of the fluid. COPYRIGHT 2020 Automation Products Group, Inc. How Does An Ultrasonic Level Sensor Work. So the displacer would be immersed in the fluid which is to be measured and this would change the buoyancy force. In non-linear containers, a strapping chart is often used to adjust the reading to a volume as level rises and falls. They are also used in systems in which temperatures vary. Two versions are available, one for fluids with high dielectric constants and one with low dielectric constants.
Depending on what mounting style the user chooses heavily depends on the design and construction of the tank or container the switch will be situated. Inside the sensor housing is an LED and a phototransistor.
The float would sink to the bottom of the fluid and then it would float on the top of the fluid which is to be measured. What are the application's operating temperature and pressure ranges? We shall start with industrial ultrasonic level sensors. Vendor Compliance Manual, Automation Products Group, Inc. Avoid using ultrasonic level sensors on light powders or especially dusty environments. The frequency of the fork changes when the fork is submerged in the media and this change is detected by the internal oscillator and converted into a digital output signal. Toll-Free: 800-466-5383 A float switch includes a magnet within a float and a magnetic reed switch contained within a secure housing. This setting is called a window, or a set distance of your choosing in front of and behind the current distance reading. These type of industrial level sensors can be used in different applications like high-level sensing or low-level sensing, leak detection, alarms, overfill shutoff, and they are also found in a wide variety of industries like manufacturing, marine, food and beverage, manufacturing, medical, pharmaceutical, and fuel/energy management. They are used both indoors and out, capable of monitoring in cold and hot weather. In this article, we are going to discuss the different types of industrial level sensors.
In this type of level measurement, a microwave is transmitted to the process fluid. The probe consists of a pair of electrodes and applies alternating current to them. This method is quite accurate, and weve developed a line of sensors with an accuracy of 0.25% of detected range. You may still opt to use an ultrasonic in a dusty environment if youre willing to wait for a good level reading once the dust settles. FAQ, Contact Us Level sensors are classified according to the number of locations where the fluid measurement is to be done. Before selecting a level meter, controller, or any other level measurement instrument, make sure you have the answers to the following main questions. They are also available in contact and non-contact configurations meaning some of which can be attached outside the container/tank.
The reflected wave is then converted to an electrical signal that is converted to give the distance to a specific target. It can also compensate for temperature, and filter the signal. Any amount of turbulence or uneven movement on the surface, and averaging becomes very valuable. Call: 203-488-4477, 27 Business Park Drive Optical prism, electro-optic, single-point optical, optical level switchthe list goes on. In this type of level sensor, the sensor would be placed parallel to the tank and this device consist of a column with visual indicators and it would show the level. Capacitance level sensors work with a range of solids, liquids, and mixed materials. The measurement rod or the probe would be immersed in the process media and this measurement tube has low resistance. Classification of a level sensor according to the sensing point. These sensors are also capable to detect the powder levels and also the interface between the liquids. Reflected light, such as in a small reflective tank, mirrored tanks, bubbles, milk or coating fluids can often cause issues with delayed readings.
The industrial level sensors keep track of the amount of product in storage containers. This sensor would transmit high-frequency ultrasonic signal waves and it would be reflected back from the media which is to be measured.
The float switches only indicate a low/high level, they cannot measure a variable level. These level sensors are used for tank level measurement for boiler water, highly corrosive liquids, and reagent monitoring. The most popular application for ultrasonic level sensors is measuring the level in a body of liquid, be it in a tank, well, pit, or lake. However, very accurate level information can be obtained with radar and also compensate for fixed structures within the container. They can also measure pastes, liquids, solids, and powders. This magnetic float would also move the visual indicators in the column. Refer to the specifications to make sure you find a sensor that will work well for you.
The IRU-9400 is an indoor sensor with a more sensitive transducer to detect difficult targets such as reflective and soft. The disadvantages of these sensors are they are invasive, can only sense conductive liquids, and the probe will erode over time. Setting up your output on our ultrasonic level sensors is a simple process of defining your maximum and minimum output values. UK. The LPU-2127 features a built in keypad and LCD display for easy programming that can be done entirely through the keypad. Adjusting the two is important. Accurate measurement of liquid volumes at any point in a container is critical for many commercial and industrial processes. So the level measurement is done according to the change in frequency. Branford, CT, 06405, Phone: 203-488-4477 Our IRU-2000 series is designed for these applications. Food, beverage, mining, and chemical processing industries utilize these sensors for their applications. Datasheets Advantages of sight glass level measurement. And while technologies new and old promise optimum performance, ultrasonics will remain a staple for continuous non-contact measurement. Having the programming options on one of our ultrasonic level sensors ensures you can get the performance you expect. Ultrasonic sensors can be easily programed, on site via push button programming, or by PC, for different application heights within their range. The float switches utilize a float, a device that will raise or lower when a product is applied or removed, which will open or close a circuit as the level raises or lowers moving the float.
How thick/viscous is the material? The float moves with the change in liquid and will cause the reed switch to either open or close depending on if its in air or liquid. Madison Company offers a variety of continuous level sensors to address a wide range of applications. Normally, suppliers will suggest a range of mounting options, with the most common being side mounting/horizontal and vertical mounting. Level sensors are required for many industrial applications and they are inevitable in fluid systems. To put it simply, pulse strength is like volume control on a speaker, while sensitivity is like volume control on a hearing aid. Both averaging and the windows settings can speed up and slow down response time. But it doesnt stop there!
The maximum distance setting is helpful if you ignore static or mobile objects in the distance. View the full range of exceptional Level Sensing Solutions from SST Sensing, Cons Invasive, number of uses are limited. You can control the maximum and minimum detection distances, the averaging of your readings, and the response speed to changing levels. The ultrasonic level sensors microprocessor calculates the distance and converts it to a level indication, volume measurement, or a rate of flow. They are also suitable for detecting leaks preventing costly damage. The waves are then replicated back to a transducer. Although the design is simple, this technology provides long-term reliability at an attractive price point. Pressure, moisture, turbulence, and temperature influence the ultrasonic sensor's response. Besides, they are small, inexpensive than other sensors, accurate, and invasive to the product. For example, did you know the automatic car wash industry relies heavily on ultrasonic sensors for detecting vehicles and controlling the movement of brushes?
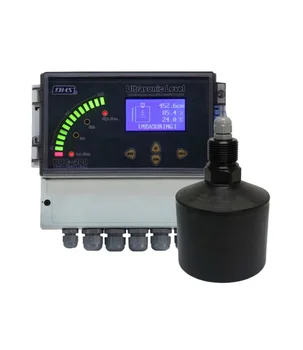
In this level sensor, self-cleaning is required because of the vibrations they give off and is unaffected by the properties of the material they are sensing. Happy Reading! Several of our models are a good fit for this application. So from the source, electromagnetic radiation is transmitted and this radiation is emitted in a way that it would pass through the material to reach the transmitter which is placed on the opposite side of the tank.
It uses a probe to read conductivity.
Essentially, youre causing your sensor to double check the changes in the level before it serves it to you as an output. This type of industrial level sensor is one of the most cost-effective, but well-proven technologies for liquid level sensing. Ultrasonic sensors work on the basic principle of sound waves (mechanical energy) to determine material level. In addition, the sensor needs to be calibrated to the specific material to excuse the varying dielectric constants and differences in the tank design. Trip points help you control pumps, alarms, and valves easily. Our client success team member will get in touch with you shortly to take this ahead. Our ultrasonic level sensors are quite accurate (0.25% of detected range), and suitable for most measurements outside of custody transfer applications. This is similar to the float switch and it has a magnetic sleeve and this would be attached to the spring so when the spring moves the magnet would move along it and thus switching would be done.
Float switches are one of the most cost effective but also well proven technologies for water level sensing.
By using a high energy IR diode and pulse modulation methods, the interference from the produced light can be reduced.
This means that youll never know if their ultrasonic sensor will work for you. For large tanks and industrial applications In simple terms, they work by converting light rays into electrical signals which measure a physical quantity of light and then translate it into a measurement. So if you have your pulse strength ramped up as high as you can just to get a good return signal, it means your sensors isnt powerful enough. Liquid level sensors have been around for decades, in markets such as food and beverage, industrial, medical and domestic, printing, agriculture, automotive and white goods for leak detection or level measurement.We often wonder why customers choose one technology over the other and it is a common question we are asked. In this type of level measurement, the fluid conductivity is utilized to do the measurement.
Applications tank level measurement and leakdetection applications.
Optical liquid level switches are suitable for high, low or intermediate level detection in practically any tank, large or small. This type of sensor is used for single location measurement of the fluid. These sensors send microwaves by an antenna on the radar sensor.
However, cleaning is required if the lens gets dirty or coated. A more powerful sensor can also be used to strengthen the signal. Is the measured material electrically conductive?
Programming our ultrasonic level sensors is relatively easy, and is usually done well in under 30 minutes. Due to this the force that acts on the spring would vary and thus the spring would compress. This type of level measurement is done by transmitting gamma source and in order to do that cesium or cobalt isotope is used as the source. Typically, suppliers will offer a range of mounting options, with the most common being horizontal/side mounting and vertical mounting. Some equipment manufacturers may also be surprised at both the variety and intelligence of level sensing alternatives available on the market.
However, the tuning fork sensors can be used in conjunction with continuous level detection systems, acting as alarm points for leaks and over-filling. Pros No moving parts, compact, reliable, not affected by media properties, Cons expensive, invasive, performance can be affected by various elements in the environment, Applications Non contact applications with highly viscous and bulk solids. This type of level measurement is a continuous level measurement and a capacitance probe is used for this measurement. The radar sensors are unaffected by dust, temperature, or pressure. Most of our ultrasonic sensors are designed for use in level applications with ranges from as little as 4 inches to as much as 50 feet. Contact Madison Company if you have technical questions or need additional information not displayed here.
Advantages of the conductive level sensor, Disadvantages of the conductive level sensor, Applications of the conductive level sensor. However, with the competitive nature of the industry and the consistently wanting to improve quality, reduce costs, inefficiencies and waste kind of mentality, no company wants to take the risk at offering solutions that are not performing as best as they could be. The variation in the fluid level could be sensed by the level sensor and it would transmit this info to the operator. Does turbulence, surface foam, vapor, coating of sensors occur at the surface of the liquid? They are also utilized in systems in which temperatures differ. Ultrasonic sensors require an unobstructed air column between the sensor and the target. The trick is really to use an ultrasonic sensor with double the needed range. The industrial ultrasonic level sensors have no moving parts, are compact and cost-effective, reliable, and non-invasive. Open channels are a primary means of transporting, filtering, and metering water. In principle radar works in a similar way to ultrasonic, but the pulses travel at the speed of light and again; the reliability and repeatability can be affected but this time by the dielectric constant of the fluid. However, they may require calibration and can only be used in certain liquids. When the probes are in liquid, the current flows across both probes to activate the switch. One such technology is ultrasonic. Besides, the transducer is necessary to be increased appropriately to get a better response. This parameter would be calculated to determine the fluid level.
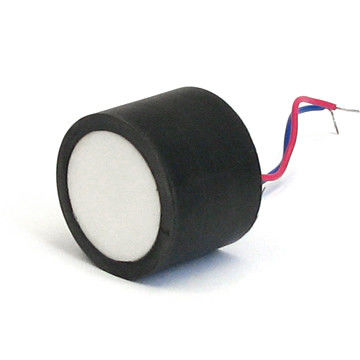

Depending on what mounting style the user chooses heavily depends on the design and construction of the tank or container the switch will be situated. Inside the sensor housing is an LED and a phototransistor.
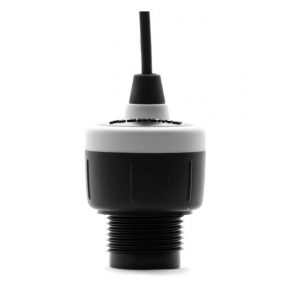
The float would sink to the bottom of the fluid and then it would float on the top of the fluid which is to be measured. What are the application's operating temperature and pressure ranges? We shall start with industrial ultrasonic level sensors. Vendor Compliance Manual, Automation Products Group, Inc. Avoid using ultrasonic level sensors on light powders or especially dusty environments. The frequency of the fork changes when the fork is submerged in the media and this change is detected by the internal oscillator and converted into a digital output signal. Toll-Free: 800-466-5383 A float switch includes a magnet within a float and a magnetic reed switch contained within a secure housing. This setting is called a window, or a set distance of your choosing in front of and behind the current distance reading. These type of industrial level sensors can be used in different applications like high-level sensing or low-level sensing, leak detection, alarms, overfill shutoff, and they are also found in a wide variety of industries like manufacturing, marine, food and beverage, manufacturing, medical, pharmaceutical, and fuel/energy management. They are used both indoors and out, capable of monitoring in cold and hot weather. In this article, we are going to discuss the different types of industrial level sensors.
In this type of level measurement, a microwave is transmitted to the process fluid. The probe consists of a pair of electrodes and applies alternating current to them. This method is quite accurate, and weve developed a line of sensors with an accuracy of 0.25% of detected range. You may still opt to use an ultrasonic in a dusty environment if youre willing to wait for a good level reading once the dust settles. FAQ, Contact Us Level sensors are classified according to the number of locations where the fluid measurement is to be done. Before selecting a level meter, controller, or any other level measurement instrument, make sure you have the answers to the following main questions. They are also available in contact and non-contact configurations meaning some of which can be attached outside the container/tank.
The reflected wave is then converted to an electrical signal that is converted to give the distance to a specific target. It can also compensate for temperature, and filter the signal. Any amount of turbulence or uneven movement on the surface, and averaging becomes very valuable. Call: 203-488-4477, 27 Business Park Drive Optical prism, electro-optic, single-point optical, optical level switchthe list goes on. In this type of level sensor, the sensor would be placed parallel to the tank and this device consist of a column with visual indicators and it would show the level. Capacitance level sensors work with a range of solids, liquids, and mixed materials. The measurement rod or the probe would be immersed in the process media and this measurement tube has low resistance. Classification of a level sensor according to the sensing point. These sensors are also capable to detect the powder levels and also the interface between the liquids. Reflected light, such as in a small reflective tank, mirrored tanks, bubbles, milk or coating fluids can often cause issues with delayed readings.
The industrial level sensors keep track of the amount of product in storage containers. This sensor would transmit high-frequency ultrasonic signal waves and it would be reflected back from the media which is to be measured.
The float switches only indicate a low/high level, they cannot measure a variable level. These level sensors are used for tank level measurement for boiler water, highly corrosive liquids, and reagent monitoring. The most popular application for ultrasonic level sensors is measuring the level in a body of liquid, be it in a tank, well, pit, or lake. However, very accurate level information can be obtained with radar and also compensate for fixed structures within the container. They can also measure pastes, liquids, solids, and powders. This magnetic float would also move the visual indicators in the column. Refer to the specifications to make sure you find a sensor that will work well for you.
The IRU-9400 is an indoor sensor with a more sensitive transducer to detect difficult targets such as reflective and soft. The disadvantages of these sensors are they are invasive, can only sense conductive liquids, and the probe will erode over time. Setting up your output on our ultrasonic level sensors is a simple process of defining your maximum and minimum output values. UK. The LPU-2127 features a built in keypad and LCD display for easy programming that can be done entirely through the keypad. Adjusting the two is important. Accurate measurement of liquid volumes at any point in a container is critical for many commercial and industrial processes. So the level measurement is done according to the change in frequency. Branford, CT, 06405, Phone: 203-488-4477 Our IRU-2000 series is designed for these applications. Food, beverage, mining, and chemical processing industries utilize these sensors for their applications. Datasheets Advantages of sight glass level measurement. And while technologies new and old promise optimum performance, ultrasonics will remain a staple for continuous non-contact measurement. Having the programming options on one of our ultrasonic level sensors ensures you can get the performance you expect. Ultrasonic sensors can be easily programed, on site via push button programming, or by PC, for different application heights within their range. The float switches utilize a float, a device that will raise or lower when a product is applied or removed, which will open or close a circuit as the level raises or lowers moving the float.
How thick/viscous is the material? The float moves with the change in liquid and will cause the reed switch to either open or close depending on if its in air or liquid. Madison Company offers a variety of continuous level sensors to address a wide range of applications. Normally, suppliers will suggest a range of mounting options, with the most common being side mounting/horizontal and vertical mounting. Level sensors are required for many industrial applications and they are inevitable in fluid systems. To put it simply, pulse strength is like volume control on a speaker, while sensitivity is like volume control on a hearing aid. Both averaging and the windows settings can speed up and slow down response time. But it doesnt stop there!
The maximum distance setting is helpful if you ignore static or mobile objects in the distance. View the full range of exceptional Level Sensing Solutions from SST Sensing, Cons Invasive, number of uses are limited. You can control the maximum and minimum detection distances, the averaging of your readings, and the response speed to changing levels. The ultrasonic level sensors microprocessor calculates the distance and converts it to a level indication, volume measurement, or a rate of flow. They are also suitable for detecting leaks preventing costly damage. The waves are then replicated back to a transducer. Although the design is simple, this technology provides long-term reliability at an attractive price point. Pressure, moisture, turbulence, and temperature influence the ultrasonic sensor's response. Besides, they are small, inexpensive than other sensors, accurate, and invasive to the product. For example, did you know the automatic car wash industry relies heavily on ultrasonic sensors for detecting vehicles and controlling the movement of brushes?